Agricultural Robotics & Off-Road Mobility
Research & Development & Engineering
Within the "i-SMART" Associated Partnership Laboratory
INNOVATIVEAND SUSTAINABLE METHODSFOR AGRICULTURAL ROBOTICS AND OFF-ROAD MOBILITY
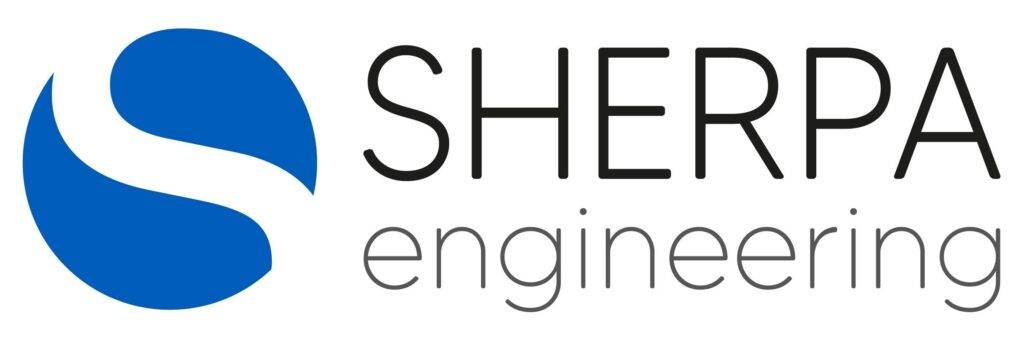
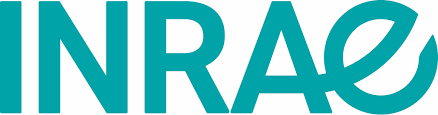
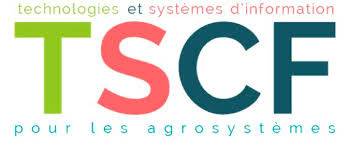
As part of the AgroTechnoPôle’s activities, SHERPA-Engineering (an ATP Innovative Company) and the TSCF Research Unit (an INRAE laboratory) have decided to forge a closer research partnership for the Development of tools and methods for the development of agricultural robotics by creating Laboratoire Partenarial Associé i-SMART (LPA i-SMART).
The LPA was signed on March 13, 2023.
Co-directed by :
The aim of the program is to develop solutions for the design and evaluation of high-performance agricultural robotic systems that will help limit the environmental footprint of the agricultural practices that mobilize them, while meeting the necessary safety and operating performance requirements.
The program is structured around 3 main themes:
- The first theme aims to develop IT tools and methods for assessing the environmental performance of agricultural systems, using life-cycle analysis coupled with systems engineering methods for modeling complex agricultural systems.
- The second theme aims to produce methods for physical testing of robotic systems, which can then be used as references and/or standards.
- The third theme deals with the development of digital tools that faithfully reproduce the robots, environments and physical methods developed in theme 2, as well as true digital twins to validate new agricultural robot solutions in their environments and tasks.
Once developed, these tools and methods can be offered as services to manufacturers, industry players and the scientific community.
The three Themes in more detail
Theme 1: Tools for assessing the environmental sustainability of complex systems by coupling LCA and systems engineering.
Scientific managers :
- Marilys Pradel, Research Engineer, UR TSCF
- Fabien Gaudin, Systems Engineer, SHERPA-Engineering
This project responds to the growing expectations of manufacturers of agricultural machinery in general, and of agricultural robots in particular: the need for criteria for assessing the environmental impact of their new products, not only during use (e.g. impact of new low-carbon engines, use of machines in an agro-ecological context), but also during eco-design at the start of the life cycle (e.g. impact of using certain types of materials) or recycling at the end of the life cycle.
This project is a perfect example of the real complementarity between INRAE-TSCF and SHERPA-Engineering, with INRAE-TSCF’s expertise in LCA and associated description and analysis tools AND SHERPA-Engineering’s ability to model/represent machine operation at different levels (complete assemblies, specific functional sub-assemblies, specific components).
The combination of LCA and systems engineering makes it possible to offer a truly original method and tools for closely qualifying a new machine in absolute terms, but also in relative terms by comparing it with existing machines.
The tool currently being developed (O-AMIE) will be used to evaluate farming itineraries using robotized agri-equipment in comparison with conventional itineraries, whether conventional or agro-ecological.
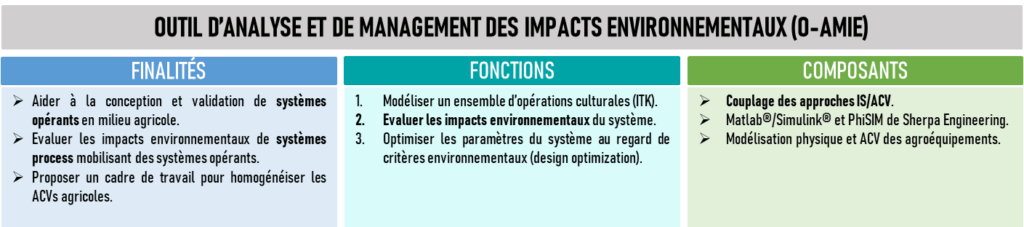
Theme 2: Development of tools and methods for evaluating the performance and safety of agricultural and off-road robots, using physical tests and expert assessments.
Scientific managers :
- Philippe HERITIER – INRAE-TSCF
- Dieumet DENIS / Fabien GAUDIN / Johann CADOT – SHERPA-Engineering
The safety and performance of mobile agricultural and off-road robots are major concerns for all players in the industry, from manufacturers to users.
The aim of this theme is twofold:
- Develop test methods and protocols to validate safety requirements through physical testing, and more generally to evaluate the performance of the robotic system in carrying out different tasks.
- Providing expert advice on design files with regard to operational safety, requirements and validation plans.
This theme extends and reinforces all the activities carried out by INRAE-TSCF and its partners CEREMA, AgreenCulture, SITIA, Vitibot as part of the ARPA (Agricultural Robot Performance Assessment) project conducted between 2019-2020 within the DIH agROBOfood (European Networks to Accelerate Agricultural Robotics) with the proposal of three initial protocols to qualify the safety of agricultural robots:
- ARPA1 - Detecting and avoiding collision with reference obstacle ISO 18497
- ARPA2 - Qualification of perception systems in disturbed environments (rain, fog, night)
- ARPA3 - Testing devices (physical or virtual barriers) to keep robots in their work zone (Geofencing)
These protocols have been identified at international level within the framework of the ISO 18-497 and OECD Working Groups.
Theme 3: Digital twins - Development of digital tools and methods for evaluating the performance, safety and development of agricultural and off-road robots.
Scientific managers :
- Christophe Debain – INRAE-TSCF
- Fabrice Peyrin – SHERPA-Engineering
The aim of this project is to set up a digital twins workshop to meet the needs of the various players involved in the development of off-road robots.
The digital twins workshop currently under construction will be based on an “Open-source” Offer 1 aimed at the research community, using free software (Gazebo, Carla), and on an Offer 2 based on licensed software, mainly aimed at industry (manufacturers, equipment suppliers, etc.), while respecting the confidentiality of future external applicants/partners.
This workshop will include digital modeling of the entire Montoldre experimentation site (outdoor and indoor development zones) of the AgroTechnoPôle, common to the 2 offers above.
The digital twins workshop will be able to meet the demands of the various players involved in the development of off-road robots, adapting to each requirement in terms of modeling accuracy or simulation level (MIL, SIL, HIL). It will be based on a simulation core, the aim of which is to organize and synchronize the various existing simulation tools – including those used by customers. The robots/vehicles and associated tools can be integrated in a variety of ways using descriptive modules. It will also have a set of models for proprioceptive and exteroceptive sensors – including models of interactions with the environment for the latter. The system will also include scenario management and data-logging tools to assess the performance of robots and other vehicles in their working environments. Initial case studies (e.g. ARPA 4 trials) will illustrate the contribution and role of these new tools/virtual environments in the design and performance evaluation of agricultural machinery.
Examples of projects within the I-SITE CAP20-25 - CIR ITPS - AgroTechnologies theme
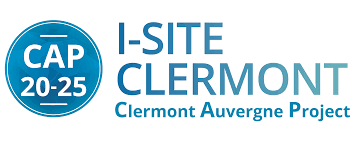
Les projets présentés illustrent des travaux réalisés dans le cadre de l’ISITE CAP20-25 et plus particulièrement au sein de son CIR ITPS / Thème AgroTechnologies qui permet aux équipes clermontoises de disposer de soutiens pour la conduite de projets amonts pour le développement, l’exploration de nouvelles technologies et de nouveaux services au bénéfice de la transition agroécologique.
Projet « SyncEA » (2019-2022)
Partners
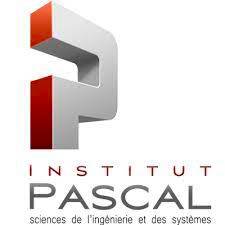
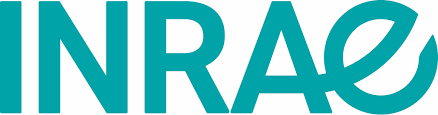
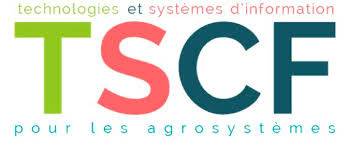
Project leader: Christophe Cariou – TSCF Research Engineer
- Dissertation Guillaume PICARD (2018-2022) entitled "Generic approach for the coordination of mobile manipulators in natural environments".
- Dissertation Omid AGHAJANZADEH (2018-2022) entitled "Control of linear deformable objects for robotic crop handling".
The SynCEA project focuses on the dynamic coupling of the movements of a robot’s mobile base (ground movement) with the movements of its on-board manipulator arm.
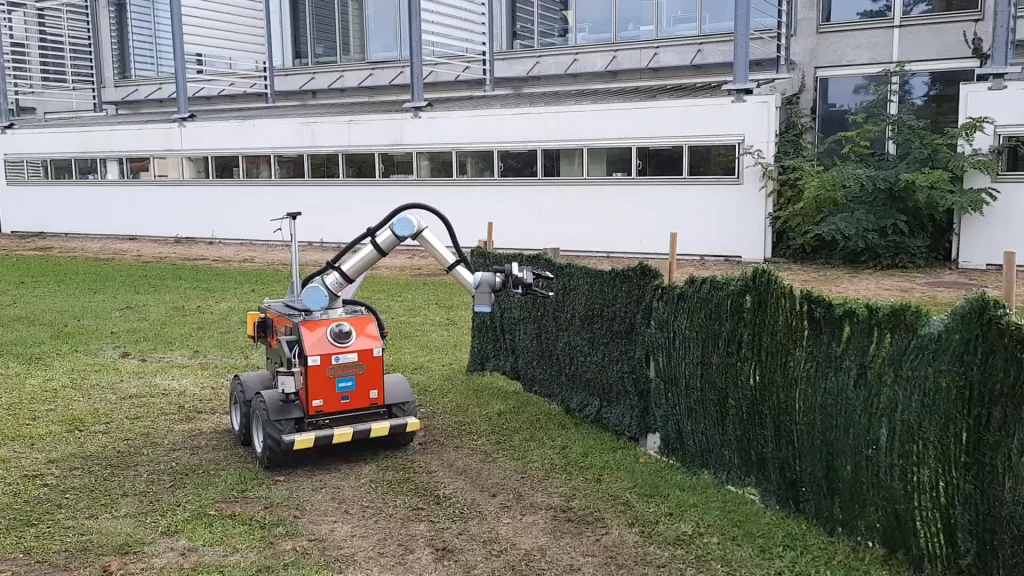
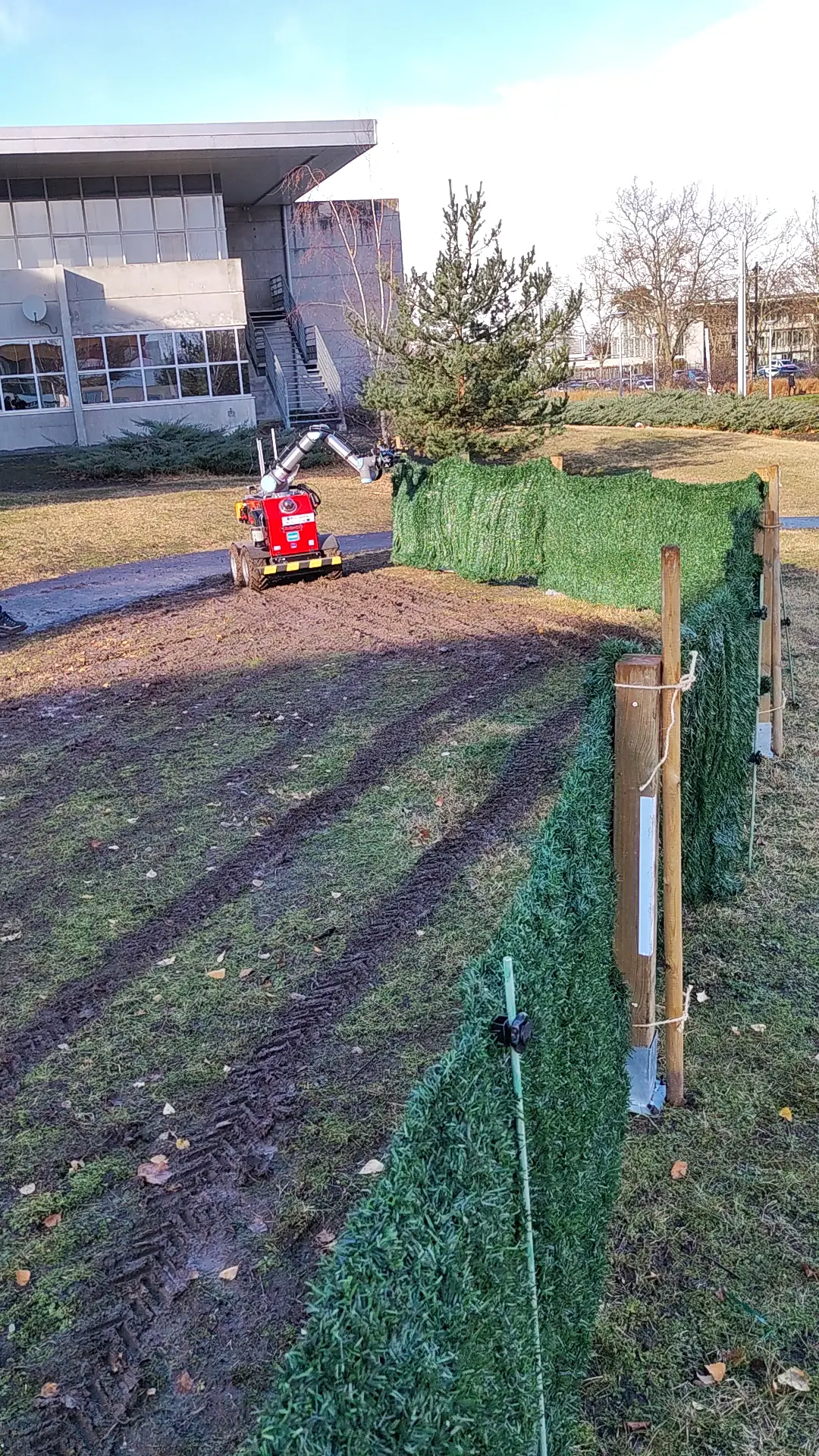
[Thèse Guillaume Picard -2018-2022 – TSCF] Coordinated movement control (moving platform/peripheral arm) for dynamic positioning of the end of the arm with respect to the distance to the row of vegetation to be followed with high precision and in the presence of natural terrain (slopes, landslides)
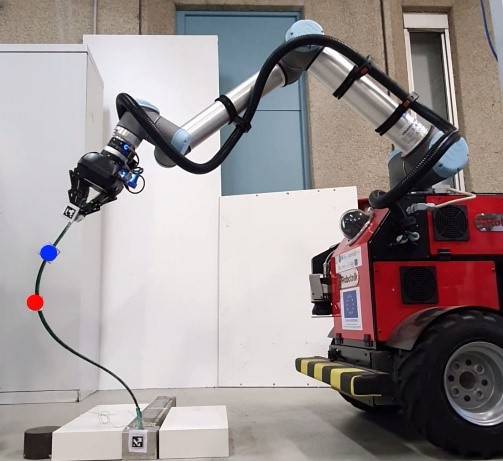
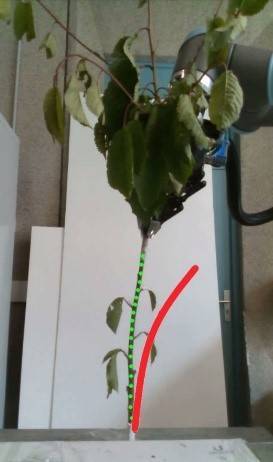
[Thèse Ohmid 2018-2022 – TSCF] Coordinated motion control (moving platform/peripheral arm) for deformable objects – The approach enables the robot to manipulate the object without any prior information on its deformation. The method can follow a desired handling trajectory to reach the target shape, resulting in smooth deformation without abrupt movements.
The application challenges related to dynamic synchronization of the robot’s rolling base with its manipulator arm(s) in complex, random and dynamic environments are high-potential.
Examples include :
- Scrutation / fine observation for disease detection
- Treatment by bio-control application
- Harvesting according to maturity
SuperROB & SEMCAR" projects (2019-2022) Management and supervision of long-distance, in situ fleets of agricultural robots based on open-source software tools.
Partners
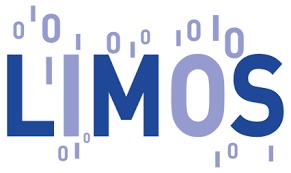
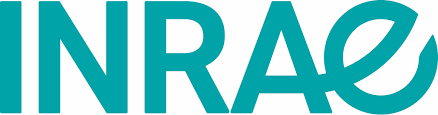
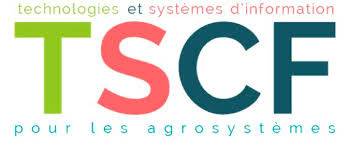
Project leaders: Sandro BIMONTE (Research Director UR TSCF) and Nicolas Tricot (Research Officer UR TSCF)
Today’s agricultural robot manufacturers are well aware of the need to go beyond the physical robot, and to associate various software tools with their machines (for example, to automatically map plots, collect data and thus enrich knowledge bases linked to the movements of the robot(s) and data linked to associated tools, ensure remote monitoring, etc.).
As the range of robotic products expands to perform different tasks throughout the production cycle, robot end-users will in future be less and less satisfied with captive solutions (hardware and software from a single manufacturer), which are the only ones available today in a nascent market.
It is therefore necessary to develop “services” in the context of agricultural robotics. (e.g. initialize, launch and monitor the execution of the mission carried out by one or more robots within the same plot, from the same manufacturer but also and above all from different manufacturers) thanks to the use of robotics, IoT and agronomy data via open source Big Data architectures.
From 2020 to 2022, the Clermont-Ferrand CAP20-25 I-SITE (led by the Université Clermont-Auvergne and involving various academic partners) supported the SupeRob project, then SEMCAR, involving INRAE’s TSCF Research Unit, UCA’s LIMOS laboratory and international partners (Italy, Tunisia). A first skeleton of a generic architecture for real-time monitoring of autonomous agricultural robots and other IoT data has been produced, called LambdAgrioT. This architecture is made up of three main layers (Edge, Fog, Cloud) that enable it to analyze data in real time, coordinate data from different devices and vehicles, and store and analyze historical data. LambdAgrIoT enables real-time monitoring and control of robot activities and management in an open source environment/system. It allows all types of robots and sensors to be integrated into this management/supervision system. This open-source architecture represents a first step towards a flexible, interoperable data management system for robots.
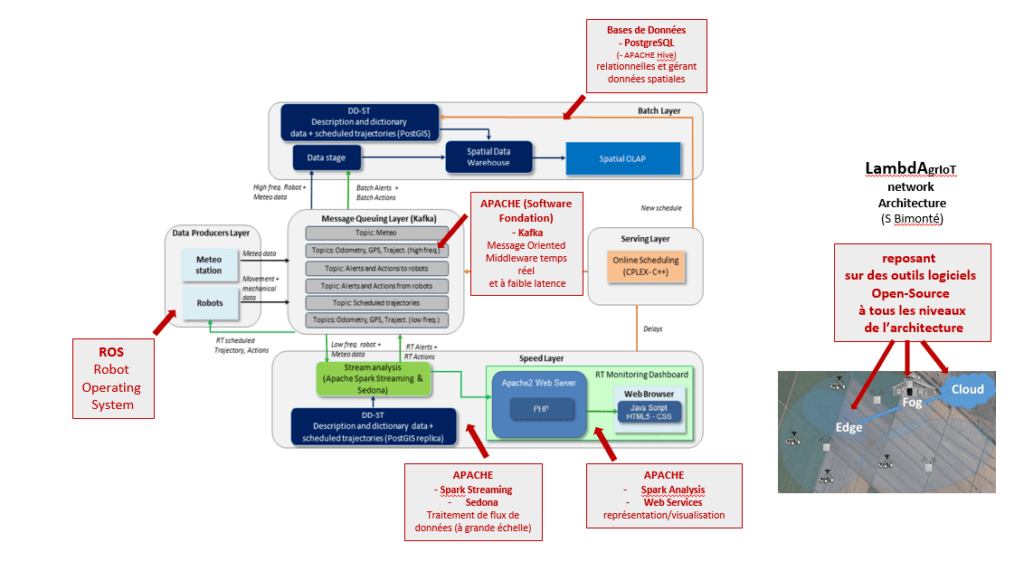
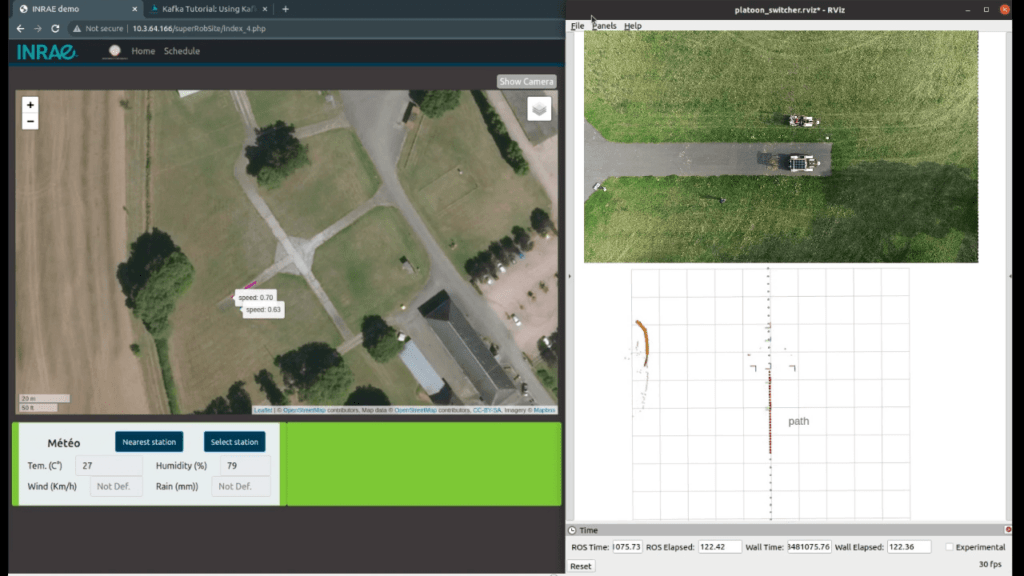
Tests
Already available with existing resources
Qualification testing of on-board safety devices on agricultural robots
The development of autonomous off-road agricultural vehicles and robots means that the safety dimension must be taken into account. It is therefore essential to set up assessment procedures to characterise the various safety devices/organisations of agricultural robots.
The work of the European ARPA (Agricultural Robot Performance Assessment focus on Safety functions) project (2019-2020) conducted as part of the DIH AgROBOfood by INRAE with the involvement of several players (CEREMA, SICK, IFM, Agreenculture, Sitia, Vitibot), has resulted in the development of three initial safety protocols for agricultural robots.
- ARPA 1 - Qualification of perception systems in relation to the ability to detect the reference obstacle defined in the first version of the ISO 18497 standard published in 2018
- ARPA 2 - Qualification of perception systems in disturbed environments (rain, fog, night)
- ARPA 3 - Testing devices (physical or virtual barriers) to keep robots in their work zone
In 2022, INRAE-TSCF and SHERPA-Engineering, as part of their joint i-SMART laboratory, will be working on a fourth protocol.
- ARPA 4 - Tests in agricultural environments (rows of vines, trees, tall crops) of dummy detection in different configurations
ARPA1 - Qualification of safety systems providing obstacle detection and robot safety functions (ISO 18497 reference obstacle).
The aim of this test protocol is to qualify the performance of on-board detection systems on agricultural robots. This test service is provided by test operator Sherpa Engineering. The test protocol was developed based on ISO 18497 – version 1 published in 2018. (See extract below)
Target market: Manufacturers of agricultural robots and, more generally, off-road robots (civil engineering, civil security, forestry machines) and equipment manufacturers offering safety systems.
Field Reference tools for dynamic positioning of machinery
This test uses a laser tracker to achieve spatial accuracy (X,Y,Z) of 10 micrometres at an acquisition frequency of 1 kHz.
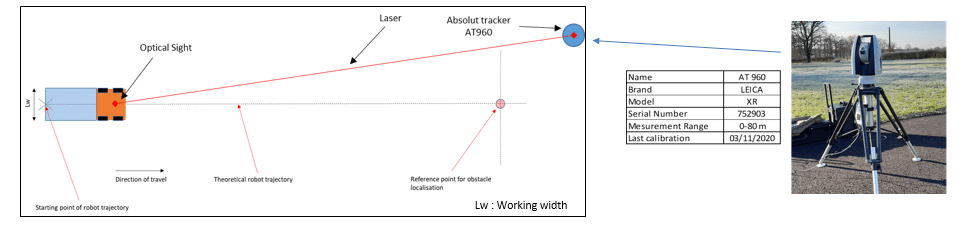
ARPA2 - Qualifying perception systems in harsh environmental conditions (rain, fog, night).
This test protocol is carried out by CEREMA, the partner and test operator, in its PAVIN – Pluie et Brouillard facility at its Clermont-Ferrand Centre – Zone du Brezet.
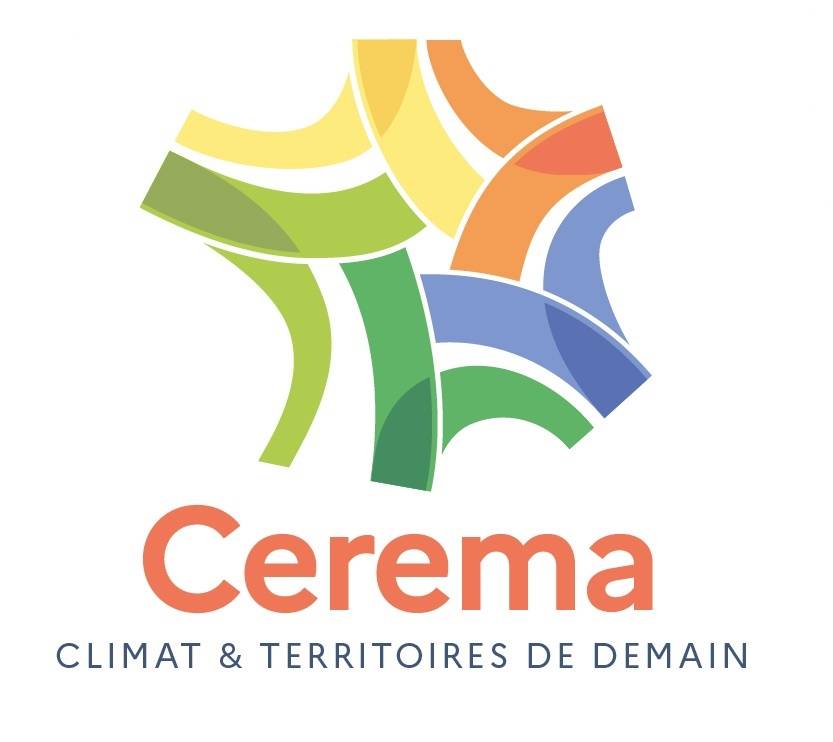
The perception systems are placed statically at the end of a tunnel, either on a support provided for this purpose, or directly on the vehicle. Different types and types of obstacle are placed at different distances from the sensors to be tested.
The principle of the test is to test the vehicle or agricultural robot under different weather disturbance conditions:
- For rain, 5 levels of rain density can be generated
- For fog, the chamber is brought to saturation and then measurements are taken throughout the dispersion time.
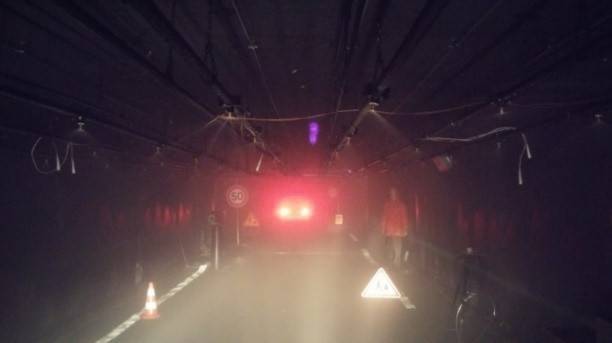
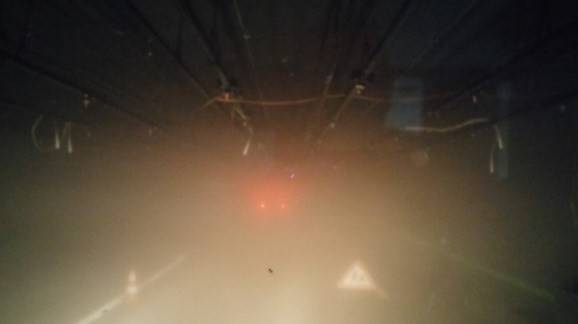
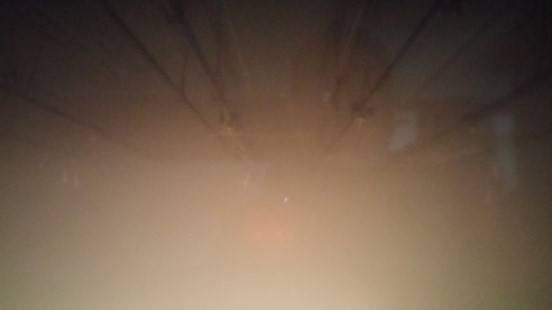
ARPA3 - Qualification of safety functions ensuring robots keep within their working area (using physical or virtual barriers).
This qualification test for physical or virtual geofencing barriers is being carried out by test operator Sherpa Engineering.
The test protocol is based on 3 qualification modes:
- Mode 1 consists of having the robot follow a trajectory designed to cover the entire given zone.
- Mode 2 involves moving the robot along the edges of the zone and checking that it does not cross the boundary line
- Mode 3 is designed to check that the robot stops when it is asked to cross the edges of the zone.
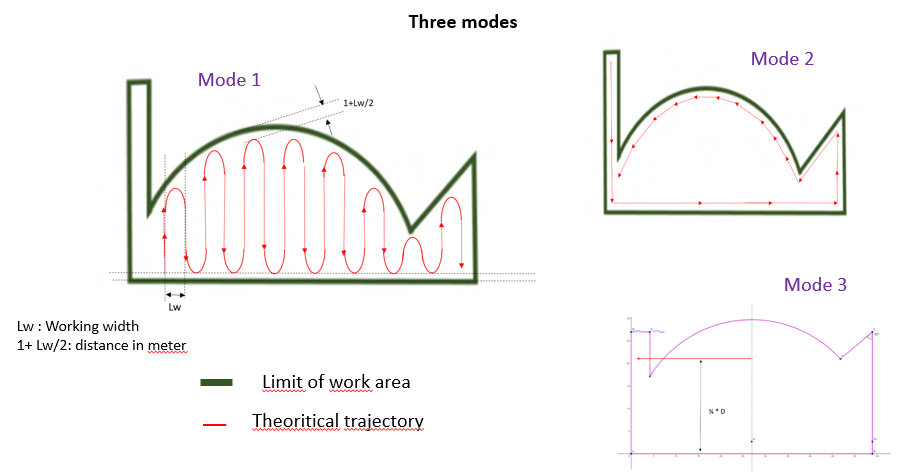
Here, SITIA and VITIBOT carry out the test in mode 1 (the videos are accelerated)
Here you can see the AgreenCulture machine performing the test in mode 2. It follows the edges. The machine is tracked by an absolute laser tracker and a drone.
ARPA 4 - Qualification of safety systems for human detection and collision avoidance, in different reproduced working environments (rows of vines, trees, tall crops).
Tests to characterise the performance of agricultural / off-road robots using field reference tools
The AgroTechnoPôle platform also offers the possibility of carrying out tests on the behaviour of “autonomous” or “non-autonomous” vehicles and agricultural machinery, thanks to the different development zones available on the Montoldre experimental site.
Characterisation of the precision of trajectory execution in difficult out-door situations (slopes, slippage, high speeds) under controlled conditions on different inclined profiles (slopes of 10% and 20%) in the line of work and during manoeuvring phases.
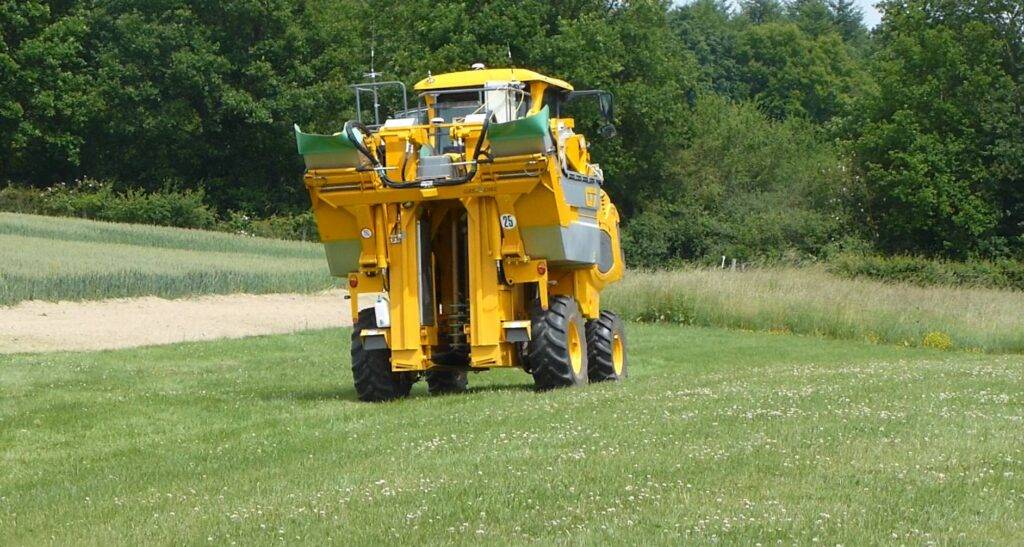
Characterisation of trajectory execution precision in difficult indoor situations (corridor, farm and semi-farm buildings) under controlled conditions.
Accuracy testing of on-board tool trajectories on a mobile robotic base (3D detection/positioning actions, harvesting actions)
Available by the end of 2024, with new resources under development
Tests to characterise the performance of agricultural / off-road robots using field reference tools
Crossing tests on steep slopes (45%, 60%)
Endurance tests in large, safe, on-demand areas
(negative and positive obstacles, fixed and mobile, rows of artificial vegetation of various types, etc.)
Dynamic load tests in controlled environments
(ISO 5008 excitation tracks) (e.g. calibration of perception systems, dynamic behaviour, etc.)